SUBJECT: |
HOW TO REMOVE DIFFICULT SOILS FROM SENSITIVE SUBSTRATES IN A WASHING PROCESS
Who Designs and Assumes Responsibility for the Washing Process?
Presentation by Gary Minkin, MART President, at the Rosemont Center in Rosemont, Illinois, at the Clean Tech 2001 Trade Show and Seminars
|
GOOD MORNING. Thanks to all of you for attending this discussion. And thanks to the CLEAN TECH folks for inviting me to present this very important issue.
In my presentation this afternoon I will discuss rebuilding as well as new manufacturing cleaning applications. It is important to note that, in most cases, no matter how dirty the materials are at the beginning of the cleaning cycle, the results must be the same in either case. The cleaning standards to be met are often dictated by the OEMs or Government Agencies. Where no cleaning standards are mandated, common sense and the goal to produce quality products determines the standards.
We know that aluminum and zinc die cast, and the yellow metals that are soft, are all sensitive substrates. Many plastics are as well. But a sensitive substrate can also be iron and steel parts that have machined surfaces or have had coatings applied, or castings that have unusual properties that preclude the use of aggressive cleaning methods such as thermal processes or media blasting or acid. Let's first consider some simple and straightforward substrates and soils that we are all familiar with like gasoline carbon, paint and scale on automotive aluminum cylinder heads.
The simplest cleaning method is to blast off the soils in a controlled wash process that is engineered to deliver a high flow of mild chemical in solution at high impact pressure. In this case, five heads are cleaned in a 20-minute cycle and virtually all the carbon and other soils are removed. The last traces of carbon and scale can be removed by a few minutes of glass bead blasting for the entire load. The operating parameters of the process are a 6% concentration of a mild aluminum-safe detergent in solution at 185 degrees F, at a flow of 400 GPM and 400 PSI impact pressure. In other words, the process blasts over 33 tons of solution at 400 PSI impact pressure and the heads are clean. |
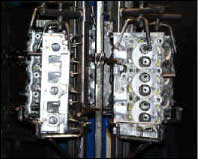 |
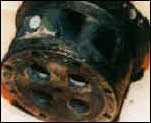 |
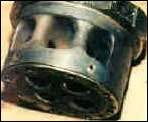 |
Systems are available to clean 80 to 200 heads in eight hours, and the process can be fully automated. Although diesel carbon is easier to remove because it contains unburned hydrocarbons, consider the exhaust ports in an EMD cylinder head that can be plugged solid with carbon. |
Removal requires the same volume of solution as gasoline carbon at half the pressure, and all traces of carbon, paint, scale, sludge and road soils are removed. With the proper pump flow and pressure, heat and caustic-base chemical, up to 12 heads can be washed in 15 minutes. Clearly an EMD crankcase does not constitute a sensitive substrate. It is made of cast iron with welded steel sides. But as with the cylinder heads, the crankcase has threaded holes and the threads must be protected. I know of one rebuilder that burns these blocks, then sandblasts them to remove the char, and washes the crankcases to remove the sand.
Burning will destroy the threads and can also cause thermal cracks that would be disastrous for the crankcase. The crankcase cannot tolerate five or six burns. The crankcase is easily washed in 1-1/2 hours to the standard you see in this picture. All carbon, scale, paint, sludge and road soil have been removed. The thread share protected, and washing cannot cause thermal cracks. The operating parameters of the wash process are 860 gallons per minute of solution blasted at 200 psi nozzle pressure, at a velocity of 168 feet per second. |
|
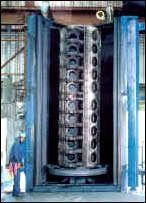 |
That's over 3-1/2 tons of solution per minute, or 315 tons of solution blasted at the crankcase over the wash cycle. Another type of carbon is the carbon brake dust on aircraft wheels. When the brakes are applied, a large cloud of carbon dust is created that embeds in the pore of the aluminum.
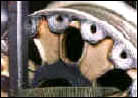 |
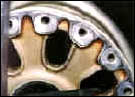 |
Aircraft wheels will also have rubber bead and, sometimes, mastic that is bonded to the inner rim of the wheel by heat and high pressure. Complicating the removal of the rubber bead and mastic is that the chemicals used in the wash process must be aluminum-safe and not cause hydrogen embrittlement. |
The bead, mastic and carbon can all be safely removed in a wash process that uses mild detergent in solution heated to 185 degrees F, and is blasted at 400 GPM and 200 PSI measured at the nozzles. Cycling time is 10 minutes for up to four wheel halves in one wash load. Some wash cabinets that are available for this work have brushes to mechanically remove the rubber bead. This method can also be effective but you should consider the replacement cost of brushes and other maintenance to the system, and whether a low powered washing machine is capable of removing the carbon dust. Ask the washer maker how its process removes the carbon. There is an additional word of caution with respect to hydrogen embrittlement.
Chemicals that have been proven not to cause hydrogen embrittlement are only safe in concentrations of 4% or less. At higher concentrations they can also cause hydrogen embrittlement. When discussing this issue with washer manufacturers, ask what chemical concentration they require to remove the soils. |
|
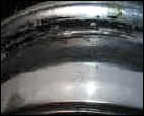 |
Low powered washing machines often need 8 to 12 or more ounces per gallon of solution to successfully clean such parts If they require a higher chemical concentration than is recommended by the chemical maker, then ask the washer manufacturer to warrant that its equipment, at the higher concentration, will not cause hydrogen embrittlement. Consider this machined valve body. The soils to be removed are chips and grindings, many of which are lodged, and cutting fluid that can be easily removed. One of the difficulties is that the machined pathways and the bore holes are smaller than the cavities inside the component, and chips and cuttings can collect in the large internal cavities that might not readily pass through the smaller bore holes. Note also that the threads can entrap the chips.
I consider this substrate sensitive because these soils must be removed without damaging the machined surfaces and threads. The best way to clean the internal passageways is by blasting solution into the cavities at high impact pressure. Note that we must take care of how we present the unit to the blast nozzles. A large chip that is lodged in the threads can pose a problem, and so can the small diameter machined hole on the left. If cuttings were lodged in the larger internal cavity, and they were dislodged and blasted towards the smaller hole, then they could easily lodge in the pathway and make removal extremely difficult or even impossible.
|
|
In this case, solution should be blasted through the smallest hole into the main body. Even then, if we simply blast straight into the hole we can shoot through the component without ever reaching the large cavity. The only ways to ensure that the large cavity is completely flushed is to blast into the entry hole at odd angles, and create a vortex or turbulence that flushes the entire interior clean.
To prove that the method I describe works, the casting was sliced lengthwise into three sections and then bolted together as a sandwich. The assembly was packed with chips and grindings - and tamped - and dipped in cutting fluid. Then the unit was properly oriented and washed, disassembled and inspected. All the chips and fluid had been removed.
Another sensitive substrate with difficult soils is this air-cooled jet engine turbine blade. The blade is a single crystal investment casting and the cleaning method must not alter the properties of the metal. The blades rotate at 30,000 RPM and can be in service for 22,000 hours before refurbishing.
While in service they pick up microscopic airborne material that embeds in the convoluted cooling pathways and can set up like rock. Discarding a heavily impacted turbine blade is not an option because the replacement cost is up to $11,000 each. All the contaminant must be removed. One extremely reliable and safe method is a washing process. These are the parameters of the process - 64 to 80 blades, or an entire set of first or second stage blades, is washed in one cycle. The wash solution is a high concentration of potassium hydroxide in water heated to 300 degrees that is blasted into the internal passages of each blade with 700 gallons of solution at 600 PSI impact pressure over two hours. The cleanliness is verified by the next step in the process, which is X-ray. The wash cycle time is 1-1/2 to 2 minutes per blade. The mold for this investment casting is cured alumina-silica so it sets up like concrete. |
|
The mold is easily lifted off in chunks with caustic in hot solution, blasted at 600-PSI impact pressure. The caustic solution attacks the aluminum that is the weakest component of the mold material. Cycle time is 20 minutes per casting.
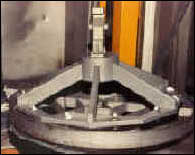 |
 |
Many manufacturers and rebuilders will paint a component before machining to end up with a crisp and very attractive unit that will have excellent customer acceptance. Here we have an engine assembly that was reconditioned in the manner I described. |
It could as easily have been a newly manufactured tractor hub or other part. Note that the machined edges are crisp and clean, and there is no overspray on the engine block or other components.
The first step was to prewash the complete engine assembly for six minutes, and then disassemble. The block and other parts were then washed a second time to remove all soils. Next the block was inspected and magnifluxed, and repaired. The repaired areas were dressed, and then the block was painted. Machining and finishing followed. The last step is washing to remove the cuttings and chips, machining oil and, if graphite lubricant was used in the machining center, then the graphite stain must be removed as well.
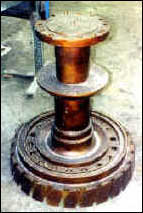 |
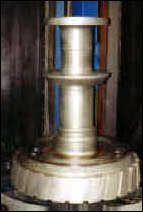 |
This cleaning is accomplished in a one to two-minute wash cycle by flooding the block with mild highly rinseable detergent in low concentration of 2 to 4 ounces per gallon, at 50 PSI and 448 GPM. In other words, each block is flushed with almost two tons of solution at low pressure and, thus, low velocity to preserve the painted surfaces. For high production applications the washing machine will be an automated pass thru style. For safe cleaning and risibility, the detergent should have as its base a potassium compound such as potassium metasilicate instead of sodium metasilicate that will be more aggressive and more difficult to rinse, and could remove some of the paint. |
Cosmolene and other protective coatings are easily removed in the wash process. But here, as with some of the other cleaning jobs we have discussed, caution must be taken to protect the substrate after the coating has been removed. Otherwise when a protective coating is removed the substrate is exposed to the elements and can corrode. And the chemical must have exceptional soil disbursing qualities so the protective coatings will not redeposit onto the parts. When dealing with coating waste, you must also address the issue of solution management because coatings tend to stick to everything and can quickly contaminate the solution and plug up the wash system. Ask the washer maker its chemical recommendation and how its process can maintain the bath so you won’t spend more time cleaning out and maintaining the machine than cleaning parts. Electric motor parts present a unique set of cleaning issues. In a rebuilding application the soils most critical to be removed are the soils between the windings and the inside of the case. These soils are difficult to get to, and they are often embedded in the windings.
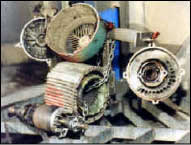 |
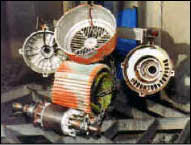 |
The washing machine must be designed to specifically clean this soiled area, and it is imperative that the manufacturer explains how its process cleans this area and removes these soils. If the soils remain after washing they can cause an otherwise properly rebuilt unit to fail. |
Note also that the wrong chemical can leave crystalline deposits that are conductive and can create shorts in the fields. Therefore, the chemical used to clean electric motors must be highly rinseable and as close to non-conductive as is practical. Most electric motor shops buy mild steel washer cabinets because of the high cost of stainless. The problem is that many chemicals that qualify for electric motor parts cleaning do not provide the necessary rust protection for a mild steel cabinet. Then too some motor shops may not maintain the proper pH so they will experience premature corrosion of the cabinet. If the chemical is appropriate for the application and the concentration is maintained, a well-manufactured mild steel cabinet should last 20 or more years.
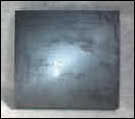 |
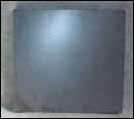 |
Silicon wafers require an extremely high cleaning standard and cannot tolerate any soil, including fingerprints, after cleaning. Large loads of wafers are cleaned with a special chemical blasted at low pressure and high flow for few minutes, and the wafers are consistently cleaned to the required standard. |
Many manufacturers use exceptionally tough paints with exceptional wear resistant qualities. The paints withstand the severe duty of extreme hot and cold climates, and all weather conditions. We see the results after blasting the parts with mild aluminum-safe detergent in solution at high impact pressure for 30 minutes. Other paints can be removed in 8 minute cycles.
TALK ABOUT COATING REMOVAL
The removal of coatings, such as baked-on enamel, epoxy and polyurethane, is difficult but it is possible in an aqueous washing system. The technology to remove coatings is new, and the chemical industry continues to research and develop new compounds and processes for their removal. At present, the parts are first pre-soaked in a solution that softens the coating so that it can be blasted off in a high-pressure wash cabinet. Soaking adds an extra step to the removal process but is still an extremely fast and reliable method, and is preferable when the coating is applied to a sensitive substrate.
WHO PICKS THE CHEMICAL?
The blends of chemicals that are available for all the different cleaning are almost infinite. Each blend works differently, but the results can be similar for a specific application. I've made some references to the variety of chemicals and this brings me to a very important question: WHO SELECTS THE CHEMICAL FOR THE APPLICATION?
Most people think that the chemical selection is their responsibility. If you believe this, then you are wrong. If you select the chemical you have let the washing machine manufacturer and chemical maker off the hook. If the machine doesn't meet your requirements and standards, the washer maker can always say, "The problem is the chemical." And the chemical manufacturer can always blame the machine. I suggest that you don't want a washing machine and you don't want chemicals - you want a cleaning process. You want clean parts. Explain your requirements and standards to the washer manufacturer in detail, and let the washer maker recommend the equipment and chemical that meets your requirements.
I recently reviewed an RFQ from General Motors - Allison Transmission Division that was the finest example of the principle I have just described. The RFQ explained in detail the methods they had tried without success, and described in greater detail the results that were required. The RFQ then required that the responders provide a detailed description of the process they would furnish that could meet the requirements of Allison Transmission. The RFQ placed the entire burden of meeting the specs on the washing machine maker, which is exactly where the burden belongs. You have an expectation of benefits to be met, and it is up to the washer maker to meet them.
When choosing a chemical, many issues come into play. First of all, the best chemical in the world is of no value if it pollutes or is unsafe for your employees. Chemical selection must be based on the complete process. This means that the chemical meets or exceeds the desired cleaning standards - it means meeting all the environmentally responsible waste disposal parameters and, at the same time, it means providing protection for the workers and the washer cabinet. Meeting all these criteria is the responsibility of the washer maker. I realize I am repeating myself when I say that you should not let the manufacturer off the hook. The washer maker must recommend the chemical for the application and warrant that the chemical will meet all the parameters I have outlined when used in the washing machine THEY recommend.
ONLY USE 100% ACTIVE CHEMICAL CONCENTRATES
I offer one additional caution with respect to chemical - make certain that the recommended product is 100% active and does not contain fillers. Fillers are inexpensive, inactive ingredients that are used to fill up the drum with low cost product to reduce the per pound cost of the compound. You end up paying less per pound and consuming more pounds of chemical to charge and maintain the bath. They drop out of solution as sludge and do not contribute to the cleaning. Note too that these inactive ingredients can interfere with the overall bath life by degrading the water quality of the solution.
Finally, you should know the quality of your water supply. All tap water has impurities. Chemicals in the water can have plating characteristics, or they can be corrosive. Either condition will alter the efficacy of the chemicals and can cause premature deterioration of the wash cabinet. It is best to measure and maintain the pH of the solution on an ongoing basis, and periodically monitor the alkalinity and conductivity of your water supply as well. High alkalinity will have plating characteristics and leave a buildup on the cabinet, plumbing, nozzles and pump system, and high conductivity will cause corrosion of the cabinet. It is the responsibility of the washer maker to advise you so you can monitor these conditions to ensure that your cleaning results are met, and that you receive reasonable economic life from your cabinet. Once you have acquired a washing machine, with the first minor signs of corrosion, advise the washer maker immediately so he can assist in resolving the issue by stopping the corrosion immediately. Remember that, if corrosion is allowed to build, it will run like a nylon stocking and is impossible to arrest. This is just one of the responsibilities of the washer maker to ensure your success with his equipment.
This concludes my portion of the discussion. I welcome your questions.
THANK YOU.
|